Mahindra & Mahindra: Implementing BPR

|
|
ICMR HOME | Case Studies Collection
Case Details:
Case Code : OPER008
Case Length : 12 Pages
Period : 1990 - 2001
Organization : Mahindra & Mahindra
Pub Date : 2005
Teaching Note : Available
Countries : Japan
Industry : Automobile
To download Mahindra & Mahindra: Implementing BPR case study
(Case Code: OPER008) click on the button below, and select the case from the list of available cases:
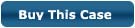
Price:
For delivery in electronic format: Rs. 300;
For delivery through courier (within India): Rs. 300 + Rs. 25 for Shipping & Handling Charges
» Operations Case Studies
» Case Studies Collection
» ICMR HOME
» View Detailed Pricing Info
» How To Order This Case » Business Case Studies » Case Studies by Area
» Case Studies by Industry
» Case Studies by Company
Please note:
This case study was compiled from published sources, and is intended to be used as a basis for class discussion. It is not intended to illustrate either effective or ineffective handling of a management situation. Nor is it a primary information source.
|
<< Previous
Excerpts
About BPR
The concept of BPR was popularized in the early 1990s by Michael Hammer and
James Champy in their best-selling book, 'Reengineering the Corporation.' The
authors said that radical redesign and reorganization of an enterprise was
necessary to lower costs and increase the quality of service. According to them,
IT was the key enabler for that radical change. Hammer and Champy felt that the
design of the workflow in most large corporations was based on assumptions about
technology, people and organizational goals that were no longer valid. They
recommended seven principles of reengineering for streamlining work processes
and, consequently, achieving significant levels of improvement in quality, time
management and cost (Refer Table I)...
|
|
M&M's Experience with BPR
By the mid 1990s, BPR had become a popular tool globally, with many leading
organizations implementing it. However, when M&M undertook the exercise, it
was still a new concept in India.
|
M&M's
workforce, as mentioned earlier, resisted this attempt to reengineer the
organization. Soon after the senior staff began working on the
shopfloors, the first signs of the benefits of BPR became evident.
Around a 100 officers produced 35 engines a day as compared to the 1200
employees producing 70 engines in the pre-BPR days.
After five months, the workers ended the strike and began work in
exchange for a 30% wage hike. As the situation returned to normalcy, BPR
implementation gained momentum. M&M realized that it would have to focus
on two issues when implementing the BPR program: reengineering the
layout and method of working, and productivity... |
The Future
Summing up the company's BPR experience, Anand Mahindra said, "Let me put it in
a simple way. If we have facilities in Kandivili today, which are not just
surviving but thriving, it is all due to BPR...
Exhibits
Exhibit I: M&M - Milestones
Exhibits II: M&M - Summary Of Operations
|
|