Six Sigma at GE

|
|
ICMR HOME | Case Studies Collection
Case Details:
Case Code : OPER015
Case Length : 12 Pages
Period : 1995 - 2002
Organization : GE
Pub Date : 2002
Teaching Note : Available
Countries : USA
Industry : Varied
To download Six Sigma at GE case study
(Case Code: OPER015) click on the button below, and select the case from the list of available cases:
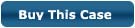
Price:
For delivery in electronic format: Rs. 300;
For delivery through courier (within India): Rs. 300 + Rs. 25 for Shipping & Handling Charges
» Operations Case Studies
» Case Studies Collection
» ICMR HOME
» View Detailed Pricing Info
» How To Order This Case » Business Case Studies » Case Studies by Area
» Case Studies by Industry
» Case Studies by Company
Please note:
This case study was compiled from published sources, and is intended to be used as a basis for class discussion. It is not intended to illustrate either effective or ineffective handling of a management situation. Nor is it a primary information source.
|
<< Previous
About Six Sigma
Six Sigma is a well-structured, data-driven methodology for eliminating defects,
waste, or quality control problems in all kinds of business activities. It is
based on a combination of well-established statistical quality control
techniques, simple and advanced data analysis methods and the systematic
training of all personnel at every level in the organization involved in the
targeted activity or process. It is based on the statistical concept that the
output of most of the physical processes follows a normal distribution,2
with the processes centered at the mean (Refer Exhibit II). Theoretically, any
process would have a natural spread of 3 Sigma (standard deviation) from the
normal distribution mean on either side of the center.
|
|
This spread contains 99.9999998% of the process output. Thus, only 0.002 parts
per million are out of the design specification. However, in practice, it is
difficult to control the processes and any typical physical process would
deviate from the natural centre by up to 1.5 standard deviation. Thus, Six
Sigma in real life denotes a defect rate of 3.4 parts per million (Refer
Table I).
|
Six Sigma
is a sophisticated quality program that is designed to reduce defects to
3.4 per million opportunities. The program focuses on streamlining all
the processes in the organization to improve productivity and reduce
capital outlays while increasing the quality, speed and efficiency of
the operations. The concept was pioneered by Motorola in the early
1980s. Motorola's initiative stemmed from its belief that improving
quality would reduce costs and that the highest-quality producer should
be the lowest-cost producer. Six Sigma enabled Motorola to achieve
defect-free performance in its manufacturing, designing, engineering,
and business processes. Six Sigma was originally developed to be used
for 'physical process' - those performed in manufacturing and easy to
observe, record, analyze and measure. |
However, in the years to come, it was extended to processes
that were not as explicit as the physical processes. It encompassed some
business areas like bid and proposal, and procurement and contract management.
While Six Sigma comprised strict measurements for physical processes, it
involved identifying waste in the form of delays for other processes. The
primary objective of Six Sigma was to increase customer satisfaction through
continuous improvement in quality...
Excerpts >>
|
|