Toyota's JIT Revolution

|
|
ICMR HOME | Case Studies Collection
Case Details:
Case Code : OPER006
Case Length : 12 Pages
Period : 1990 - 2002
Organization : Toyota
Pub Date : 2003
Teaching Note : Available
Countries : Japan
Industry : Automobiles
To download Toyota's JIT Revolution case study (Case Code: OPER006)
click on the button below, and select the case from the list of available cases:
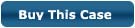
Price:
For delivery in electronic format: Rs. 300;
For delivery through courier (within India): Rs. 300 + Rs. 25 for Shipping & Handling Charges
» Operations Case Studies
» Case Studies Collection
» ICMR HOME
» View Detailed Pricing Info
» How To Order This Case » Business Case Studies » Case Studies by Area
» Case Studies by Industry
» Case Studies by Company
Please note:
This case study was compiled from published sources, and is intended to be used as a basis for class discussion. It is not intended to illustrate either effective or ineffective handling of a management situation. Nor is it a primary information source.
|
<< Previous
Background Note
Toyota's history goes back to 1897, when Sakichi Toyoda (Sakichi) diversified
into the handloom machinery business from his family traditional business of
carpentry. He founded Toyoda Automatic Loom Works (TALW) in 1926 for
manufacturing automatic looms. Sakichi invented a loom that stopped
automatically when any of the threads snapped. This concept of designing
equipment to stop so that defects could be fixed immediately formed the basis of
the Toyota Production System (TPS) that went on to become a major factor in the
company's success.
In 1933, Sakichi established an automobile department within TALW and the first
passenger car prototype was developed in 1935.
|
|
Sakichi's son Kiichiro Toyoda (Kiichiro) convinced him to enter the automobile
business. After this the production of Model AA began and Toyota Motor
Corporation was established in 1937. Kiichiro visited the Ford Motor Company
in Detroit to study the US automotive industry. He saw that an average US
worker's production was nine times that of a Japanese worker. He realized
that the productivity of the Japanese automobile industry had to be
increased if it were to compete globally.
|
Back in
Japan, he customized the Ford production system to suit Japanese market.
He also devised a system wherein each process in the assembly line of
production would produce only the number of parts needed at the next
step on the production line, which made logistics management easier as
material was procured according to consumption. This system was referred
to as Just-in-Time (JIT) within the Toyota Group.
The JIT production was defined as 'producing only necessary units in a
necessary quantity at a necessary time resulting in decreased excess
inventories and excess workforce, thereby increasing productivity.' |
Kiichiro realized that by relying solely on the central
planning approach, it would be very difficult to implement JIT in all the
processes for an automobile. Hence, TPS followed the production flow conversely.
People working in one process went to the preceding one to withdraw the
necessary units in the necessary quantities at the necessary time...
Excerpts >>
|
|