Gujarat Ambuja - Cost Leader in the Indian Cement Industry

|
|
ICMR HOME | Case Studies Collection
Case Details:
Case Code : OPEA002
Case Length : 16 Pages
Period : 2000 - 2003
Organization : Gujarat Ambuja
Pub Date : 2004
Teaching Note :Not Available Countries : India
Industry : Cement
To download Gujarat Ambuja - Cost Leader in the Indian Cement Industry case study
(Case Code: OPEA002) click on the button below, and select the case from the list of available cases:
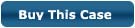
Price:
For delivery in electronic format: Rs. 300;
For delivery through courier (within India): Rs. 300 + Rs. 25 for Shipping & Handling Charges
» Operations Case Studies
» Case Studies Collection
» ICMR HOME
» View Detailed Pricing Info
» How To Order This Case » Business Case Studies » Case Studies by Area
» Case Studies by Industry
» Case Studies by Company
Please note:
This case study was compiled from published sources, and is intended to be used as a basis for class discussion. It is not intended to illustrate either effective or ineffective handling of a management situation. Nor is it a primary information source.
|
<< Previous
Excerpts
The Indian Cement Industry
In 2003, with a total capacity of 144 mn tonnes (including mini plants), the
Indian cement industry was the second largest in the world, after China. India's
cement capacity had increased from 3 mtpa in 1950-51 to around 130 mtpa in 2003,
at a growth rate of 7.6% per annum.
Between FY1992 and FY2001, the capacity
increased at an average 7.8% per annum (67 mtpa to 130 mtpa) while production
and despatches grew at 6.9% per annum (54 mt to 98 mt). Indian cement companies
had produced 111.35 million tonnes of cement, an increase of 8.7% and dispatched
111.06 million tonnes of cement, an increase of 8.5% for the fiscal year ending
March 2003...
|
|
The domestic consumption growth had been marginally lower at 6.8% per annum,
with the balance being made up by an annual growth of 27.3% in cement
exports. Rivalry in the Indian cement industry was intense with over 50
companies operating around 120 plants...
|
Manufacturing
In 2003, GACL had manufacturing plants in five different locations (Exhibit:
IV). GACL also had three grinding mills at Ropar (Punjab). GACL along with
ACC had plants in Karnataka, Tamil Nadu, Andhra Pradesh, Madhya Pradesh,
Maharashtra, Uttar Pradesh and Bihar.
The basic raw materials used in cement manufacturing were limestone, clay,
silica and gypsum. The cement manufacturing process involved four stages:
quarrying and crushing; grinding and blending of raw materials; clinker
production; and finish grinding. |
The raw materials after grinding and blending were fed into a pre-heater
followed by a kiln, which typically completed one revolution per minute. The
material flowed towards the hot end of the kiln and was heated to a temperature
of 1300-1400 degree centigrade for 1 hour.
Crushed and pulverized coal was used as the fuel. The heating process in the
kiln resulted in dehydration (removal of water vapour) and calcination (removal
of carbon dioxide). The product formed in the kiln was a dark and hard nodule,
which was cooled to form clinker. After air cooling, clinker was mixed with
retarders such as gypsum, plaster or calcium lignosulfonate...
Excerpts Contd...>>
|
|